I have built several blanket chests before but they have all been pocket hole construction. And just for the sake of changing things up a bit I decided to change up the design but try to maintain most of the same appearance. I used Google SketchUp to design the blanket chest first. Sketchup is a great tool for you to visually see the project before you even start cutting any wood. My completed design is a half lap blanket chest. I chose half laps because they are incredibly strong and relatively easy to make. To download the SketchUp file I made click here.
With the design completed I went material shopping. I am using 12 8′ 2x4s for the frame and lid.
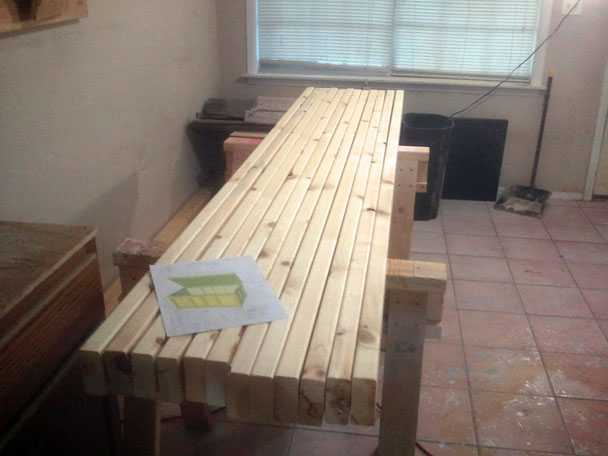
I took all of my material and cut it down to rough length for the lid and final length for the frame members. With all my pieces cut to length I needed to rip them down to final width. I went with a 2-1/2″ width. That’s pretty much what I go with on all my chests just to keep things nice and easy. And by doing so I created a lot of lattice like scraps that I have absolutely no clue what to do with.
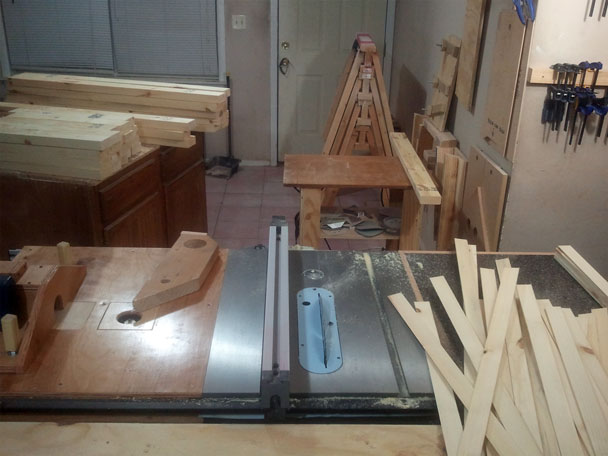
And here is the lid laid out. The lid will not be cut to final length and width until after the clue up. This way I can remove any bad spots on the ends. The final thickness of the lid should be around 1-3/8″ after all of the clean up is done. As you can see in the picture it is going to be pretty big.
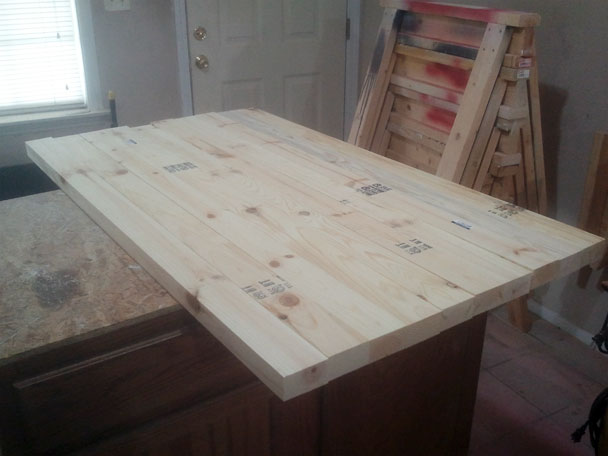
The next step is to slightly plane all of my frame material. I need to make sure they are all the exact same thickness or my half lap joints will not line up properly. I’ve got my planer set with the dust collection hose hooked up to it. And I also have an extra piece of stock that is going to go with me through the entire build. That way I have something that is the exact size that I am working with to experiment with.
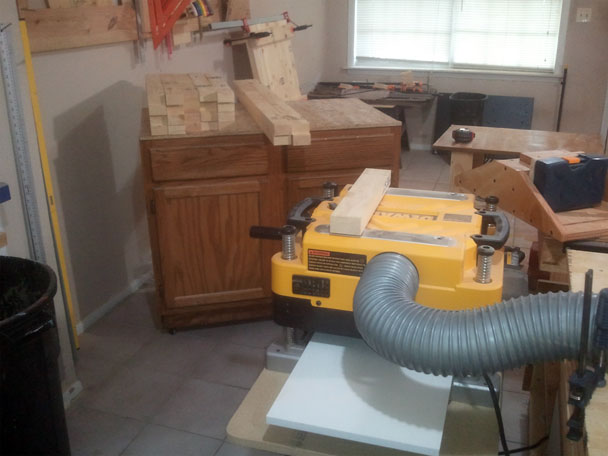
Next is the long drawn out process of cutting all the half lap joints. I will start with the end joints. Every piece will get a half lap joint on both ends.
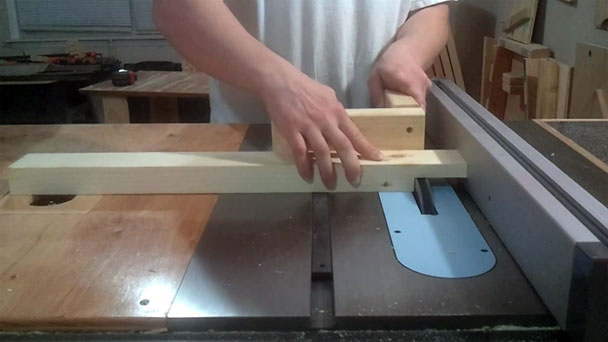
If you look at my miter gauge you can see that I have two piecs of 2x material screwed to it. One obviously to push the material through and another one in the back that runs in the same direction of as the saw blade and is lined up with the middle of the saw blade. That serves two functions. Number one, it’s a little bit of a safety reassurance. When I push through the blade is completely enclosed inside that block of wood so I can’t accidentally bump into it as I push the material through. And number two, this also acts as a dust shroud. I’m using a dado blade so I’m removing a lot of material and that’s going to stir up a lot of dust. So that helps in making sure that most of the dust goes into the cabinet itself.
With all of the half laps cut on the end of the material now I can focus my attention on the inside of all of the horizontal pieces and they need half laps as well. Because I am cutting on the inside of the pieces spacing is absolutely critical. How far I move the piece determines the width of the half lap itself, which has be 2-1/2″. This is where the kerfmaker style stop block comes in handy. What it is is 2-1/2″ minus the thickness of the dado blade that I’m using. And this allows a perfect spacing for the material to allow a 2-1/2″ dado to be cut.
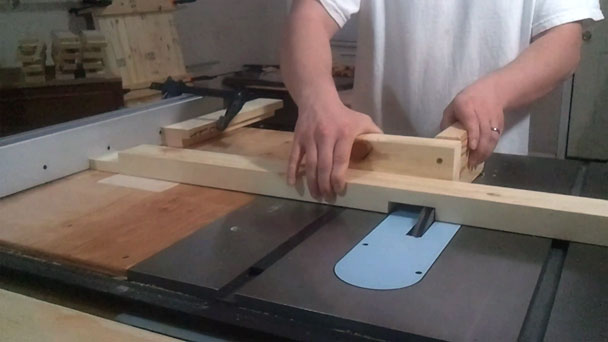
Here’s what all the pieces look like right before assembly. As you can see there’s a lot of joints here. There’s 64 cuts for each end and center sections so that makes 32 half lap joints total. A lot of work on the front end but it will be really worth it in the long run. This is going to be a very strong frame.
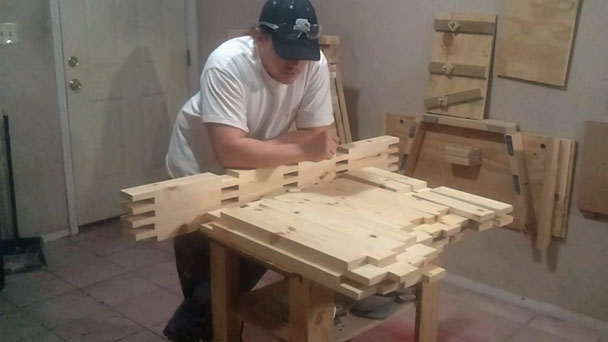
The glue up is going to be done in three different parts. My first step is to get the inside sections done and let that sit. I don’t really have that many clamps so I’ve got to do it in different phases. Once the inside pieces are done I will come back and put the legs on all four sides and then I can cut the dado into the front and back pieces that way I can assemble the whole unit. But for right now I just need to put the inside pieces together and then work on putting the legs on.
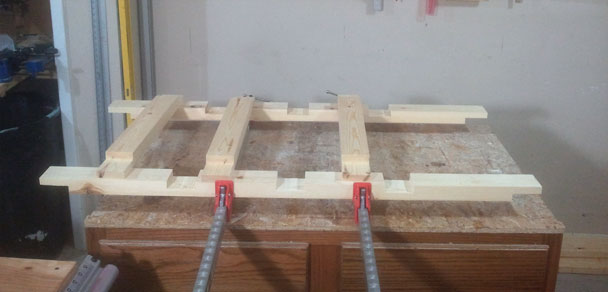
With all the structural frames glued together, starting on the inside I can start to fine tune the joints to make sure they are nice and perfect. After I get the joints cleaned up I can run them over my router table to create a rabbet on the inside of every single one of these panel areas.
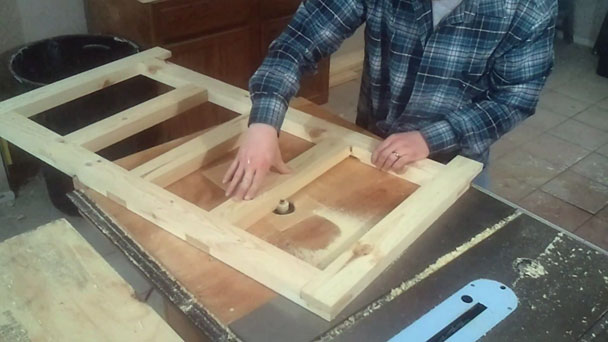
After cutting all the rabbets I need to come back and square the corners from the router bit. 48 corners total.
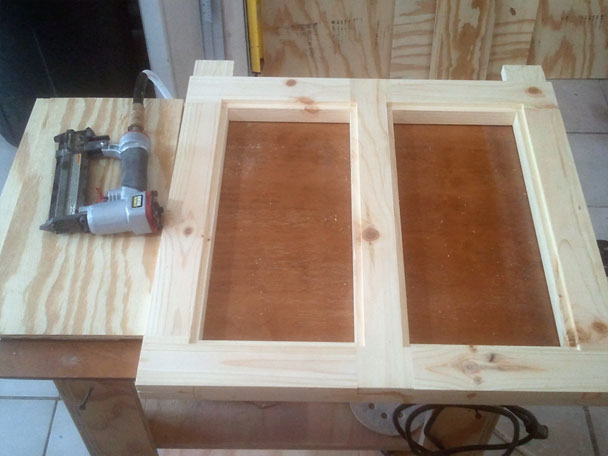
I need to not only clean up the top surfaces of all four sides because there is a half lap joint sticking out but I also need to make sure that all four sides are the exact same distance off the ground. So to do this I’ve set up a box beam level clamped to the bottom side of my side pieces and I can just run them through the table saw referencing up against the fence. This allows me to basically joint the top edge of all four sides.
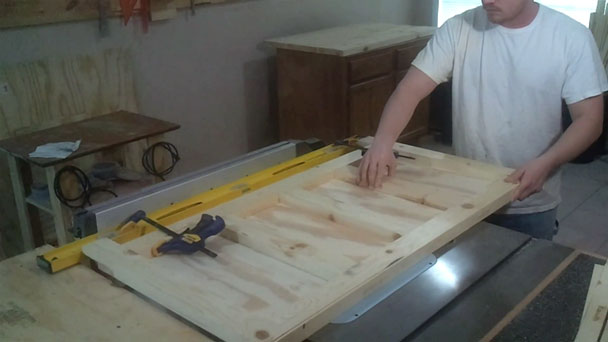
I’ve switched back to the dado blade to make the next couple cuts. Each piece needs a groove near the bottom to accept the bottom panel and it’s just going to float in place.
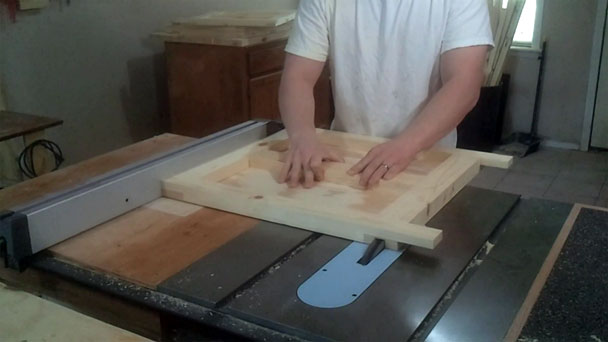
I also need to make a rabbet on the insde of the front and back to accept both side pieces.
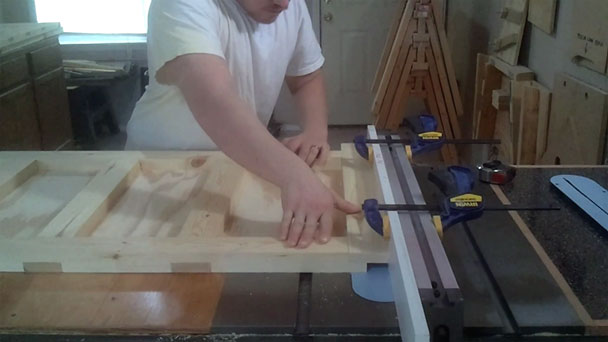
The main assembly went smoothly. I cut a 3/4″ hardwood plywood piece for the bottom panel. This panel will just float in place.
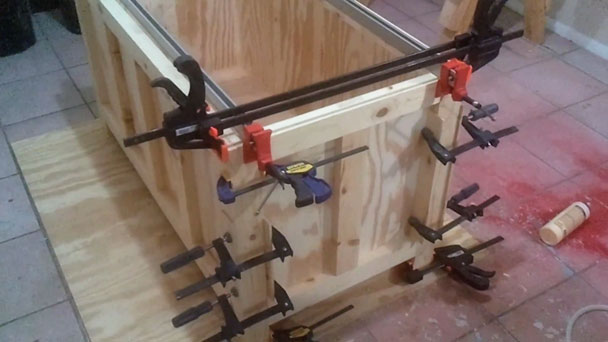
While waiting for the glue to dry on the cabinet I can work on the lid. I started with a paint scraper to remove most of the large glue squeeze out followed by my small hand plane to smooth the joints a little. I made the mistake of finishing with my smoothing plane on one side. The cheap pine I am using has the grain moving in multiple directions so I was left with a few spots of tear out. On the top side I finished with my belt sander. If you keep the sander moving in a consistent pattern you can get a decently flat surface. This is quite messy though.
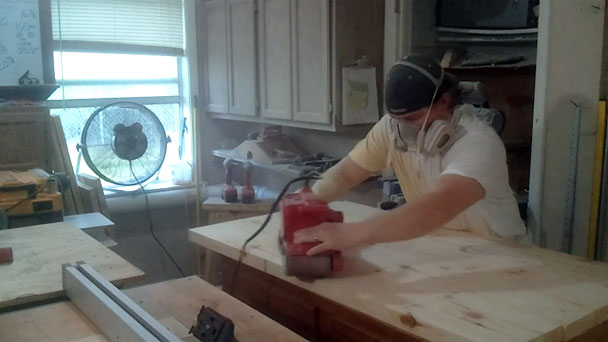
After the glue has dried on the base I can cut out the accent on the legs. I made a pattern for my router to follow. First mark out the legs. Second, remove most of the material with a jigsaw. Third, follow up with a flush trim router bit.
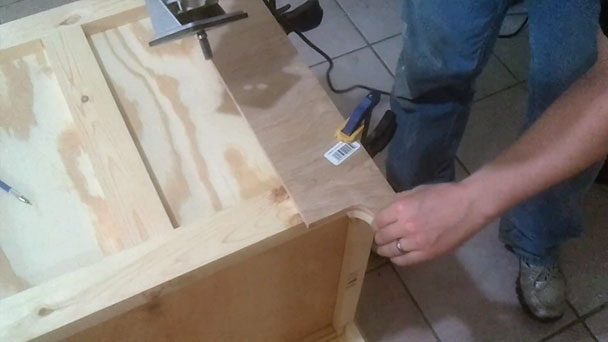
Before cutting the cove on the lid I needed to cut it down to final size. To do so I positioned it on the base and marked it’s position from below with a pencil. I outlined this mark by one inch and used my circular saw with a straight guide to cut it to size. The cove cut is made on the table saw. I am using the outside two blades on my dado stack to make the cut. I find that using the two smaller diameter, and thicker blades greatly reduces vibration during the cut. I clamped a scrap piece of dimensional lumber over the blade opening on an angle to produce the cove I wanted. After a few test passes and adjustments I was happy with the results and could cut the lid.
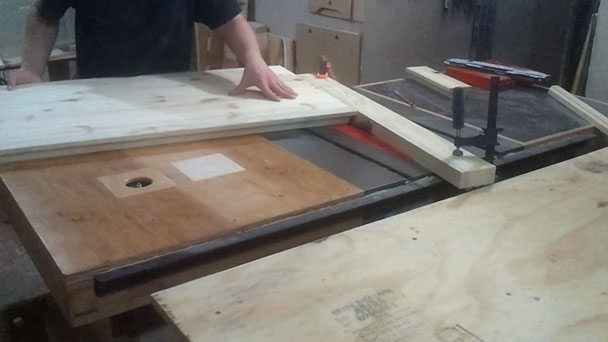
With the lid and cabinet done I brushed on two coats of clear lacquer. I knew I had a few days where I wouldn’t be able to finish the project so I decided to get ahead by putting a few coats of finish on and letting them dry in the mean time. After that I started mounting the hinges. From here out you can see a difference in image quality. No, I didn’t get a new camera. I took my camera apart and cleaned out all the saw dust that was in the lens cover. What a difference.
To mount the hinges I start by tracing the hinge with a razor blade. I then deepen the grove with a chisel and remove the bulk of the material with a router. Then I can clean up the remaining bits with a chisel again. To make perfectly centered pilot holes I use a #2 or #3 phillips bit to make a counter sink followed by a brad nail to drill the holes. This method works amazingly and can be seen in greater detail on video 3 of my shoji frame build.
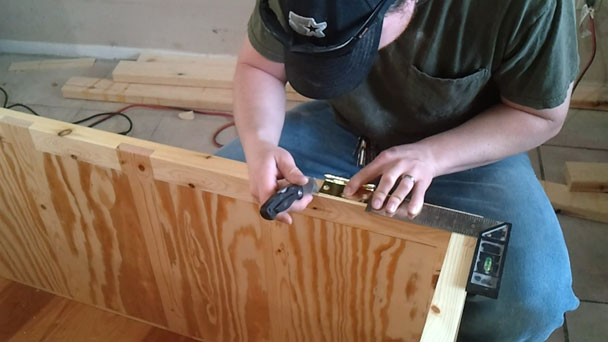
After the hinges and lid were mounted I brushed another coat of lacquer on the entire project followed by 2 more coats on the lid.
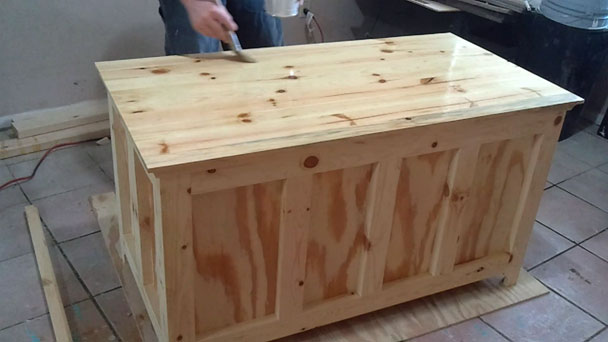
I am very happy with the results on this build. While it was a rather tedious build I still enjoyed it and learned a lot as well. I hope you have enjoyed following along and I will leave you with a few pictures followed by a quick, comprehensive video covering the build. Thanks for stopping by!
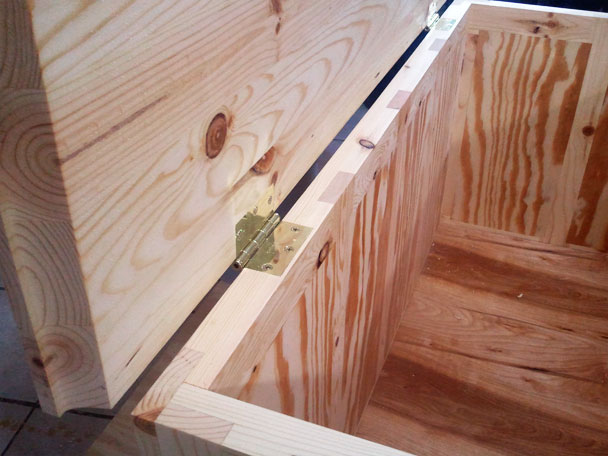
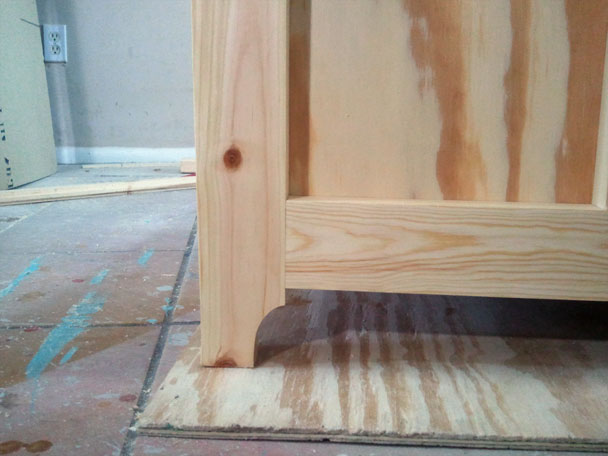
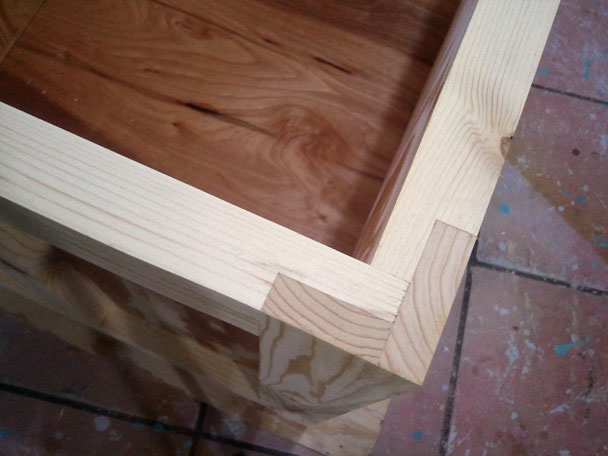
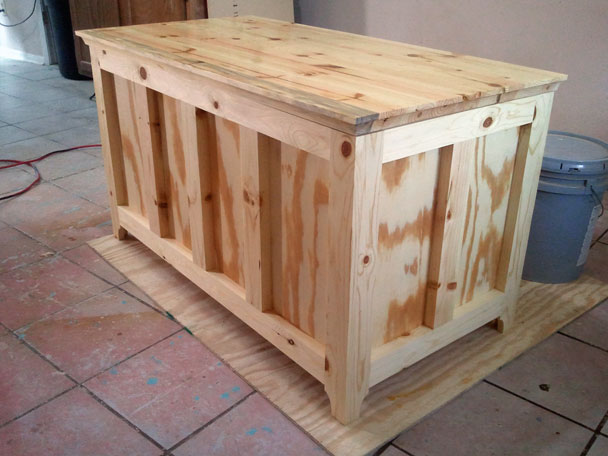
Original article and pictures take http://jayscustomcreations.com/2013/04/half-lap-blanket-chest/ site
Комментариев нет:
Отправить комментарий